
#NEXTAR R C PLANE FULL#
PivotFlex Wing Mounting System fastens with one nylon bolt, a rubber retainer and pivoting channel absorb minor jolts of normal use, more severe jolts cause the wing to separate from the fuselage and escape the full force of impact. One-piece, all wood precision airfoil with SpinControl Airfoil Extensions that provide lift even in a stall to keep the NexSTAR level and the pilot in control.
#NEXTAR R C PLANE HOW TO#
We've done tons and the electric guts are pretty easy and straight forward once you learn how to solder. My son is a great pilot so I can build planes that are out of my league to fly and he can fly the. In fact the electric plumbing is pretty much the same for all size plane conversions, just bigger components, lipo packs, ESC's, motors, etc. As far as a conversion project I'd say they are all very similar even 150 sized and even twins. If I had to chose I think I'd say that I prefer my Avistar 40 trainer as an electric flyer.
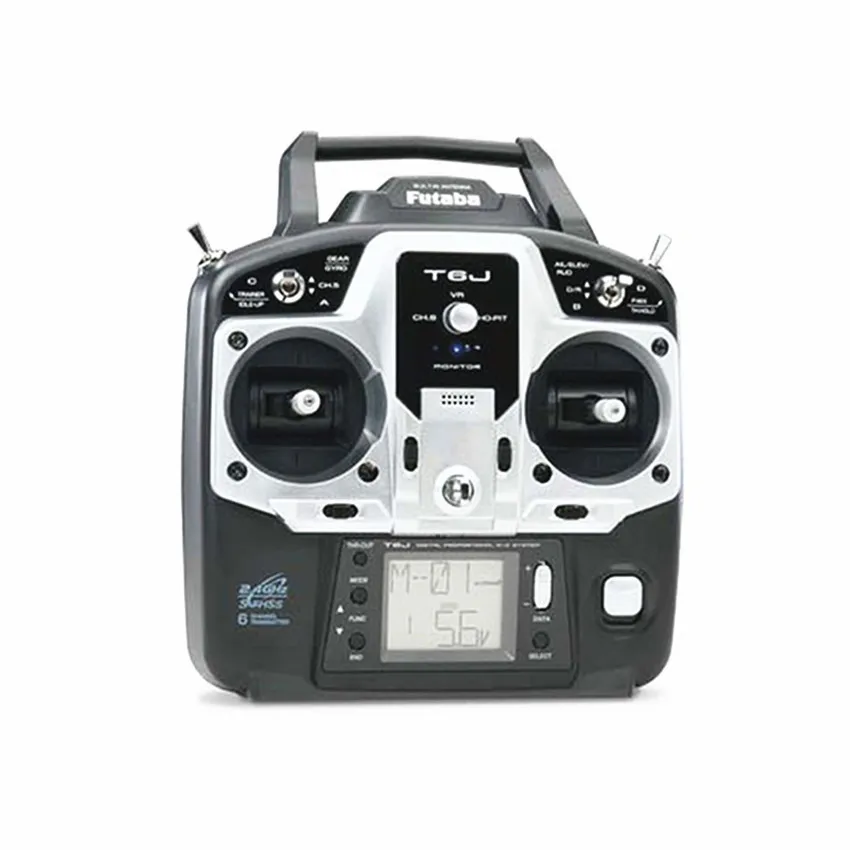
I too have trouble keeping tricycle gear running a straight line down the runway on takeoff. It doesn't race around the pattern it just flies much more like a trainer. First I mounted an Axi 4120 but the prop diameter it required was much too large for any kind of safe clearance so I downsized to an Axi 2826-12 with a 12" prop and a TP 3s (11.1volt) 4200 mAh lipo brick and it works much better than with the bigger motor.

The battery is just in the bottom of the plane up front on a pad of foam with a velcro strap. It's a bit of fabrication, but if you're good with tools it's not too bad. There are 4 long screws that go thru into the origonal motor mount blind screw, then 4 blind nuts in the back of the block that the Outrunner backplate mounts to with long screws. It's basically two layers of 1/2" balsa, sandwiched in 1/8" ply. We fabricated a block to push the outrunner reversing kit out to get the prop to the right position, and this method maintains the proper thrust angles. Now you go pick out a motor that makes that kind of power, and then match up a battery and ESC that will support it. That's all ballpark, but you get the idea. You then divide by the prop/motor efficiency, typically 75-80%, and estimate you should draw around 1050 watts (800 watts / 0.75). So, for a 8 lb plane we shoot high at 100 Watts per lb, and need 800 watts (final thrust power). That wattage range then dictates the equipment selection. For an acrobatic plane, you need 100 W/lbs min., and for 3D stunt flight you need 150 W/lb min.

You need about 50 watts per pound minimum for a trainer with simple pattern flying. On electrics, you select a power range for a given flying style, in this case a trainer is simple pattern flight. Hence, I had to put on a 15" prop to get the thrust up high enough and load up the motor. So, you can see that the 5S pack is turning too slow, and therefore to compensate you have to put a much larger diameter prop. We should target the optimum rpm for a given sport propeller around 11,000 rpm to get best results. The reality is a fresh battery with proper nominal propeller selection to load the prop to generate the thrust will draw that rpm down consideraby. So, in this case 5S is 5 x 3.7 = 18.5 volts, and 8000 mAH is two 5 cell 4000 mAH packs wired parallel. So, a 5S is 5 cells in series, and 2P means two parallel cell packs of 5 cells. Batteries (Lipo) are rated by the number of cells (3.7 volts per cell) and the capacity in mAH (miiliamp hours). That represents the RPM per Volt it will turn.
